Asphalt mixing plants serve critical roles in both precast construction and traditional road construction, yet they differ significantly in their finished mixture storage methods and transportation adaptability. These differences are essential for operators to understand, as they impact efficiency, logistics, and overall project success. This article explores these distinctions from a user-centric perspective, highlighting key aspects of storage and transportation in both scenarios.
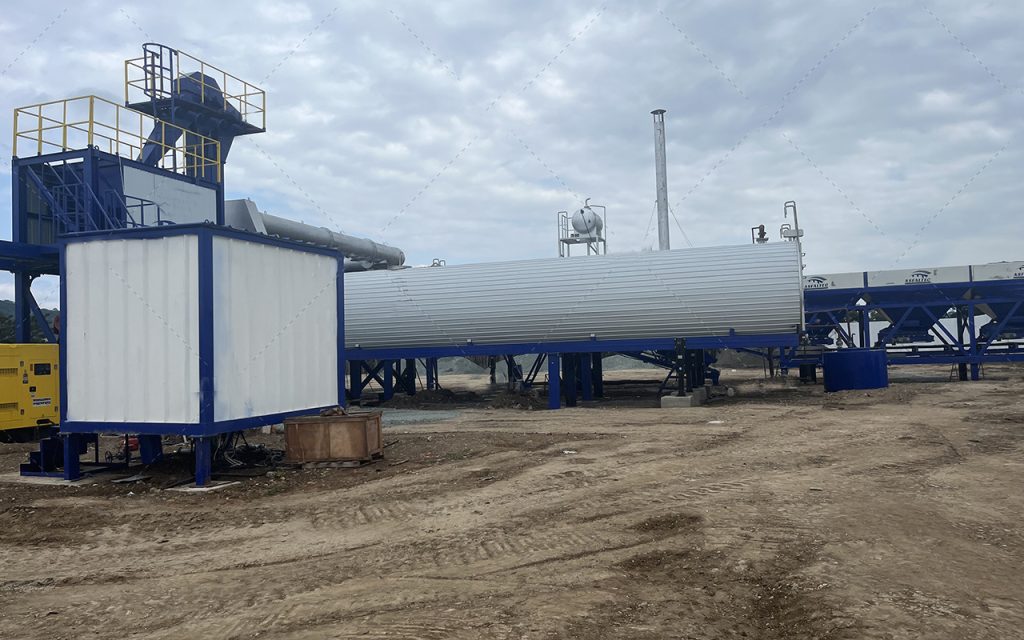
Finished Mixture Storage Methods
In traditional road construction, asphalt mixing plants typically utilize bulk storage silos to hold the finished mixture. These silos are designed to accommodate large volumes of asphalt, allowing for continuous supply to paving machines. The storage process is relatively straightforward, as the asphalt is often kept warm to maintain its workability until it is needed for immediate use on the road.
Conversely, asphalt mixing plants focused on precast construction often employ different storage methods tailored to specific project requirements. In this setting, the finished mixture is usually stored in smaller, specialized containers or bins designed for precast elements. This approach allows for better inventory management and precise control over the mix’s temperature and composition, ensuring that the specific requirements for precast components are met.
For instance, in a precast plant, the mixture may be stored in a temperature-controlled environment to preserve its properties until it is transported to the casting site. This method contrasts sharply with the bulk storage used in traditional road construction, highlighting the need for flexibility in handling various project demands.
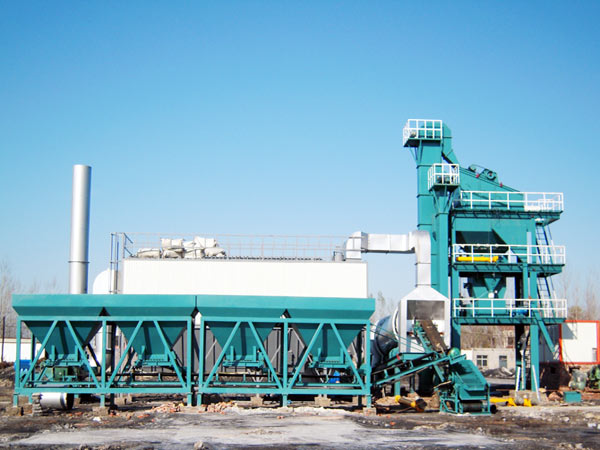
Transportation Adaptability
Transportation adaptability is another crucial difference between asphalt mixing plants serving precast construction and those for traditional road projects. In traditional road construction, the transportation of asphalt typically involves large tanker trucks that deliver significant quantities of hot mix directly to the job site. These trucks are equipped to handle the bulk nature of the material, ensuring that it remains at the appropriate temperature during transit.
In contrast, precast construction requires a more nuanced approach to transportation. The finished asphalt mixture often needs to be transported in smaller batches, depending on the specific precast elements being created. This may involve using specialized vehicles that can accommodate different types of molds and forms used in precast construction.
For example, a mobile asphalt plant for sale might be deployed at a precast site, allowing for on-site mixing and immediate use of the material. This adaptability not only improves logistics but also minimizes delays associated with transportation. Furthermore, the ability to produce smaller, tailored batches of asphalt mix on-demand enhances the overall efficiency of the precast construction process.
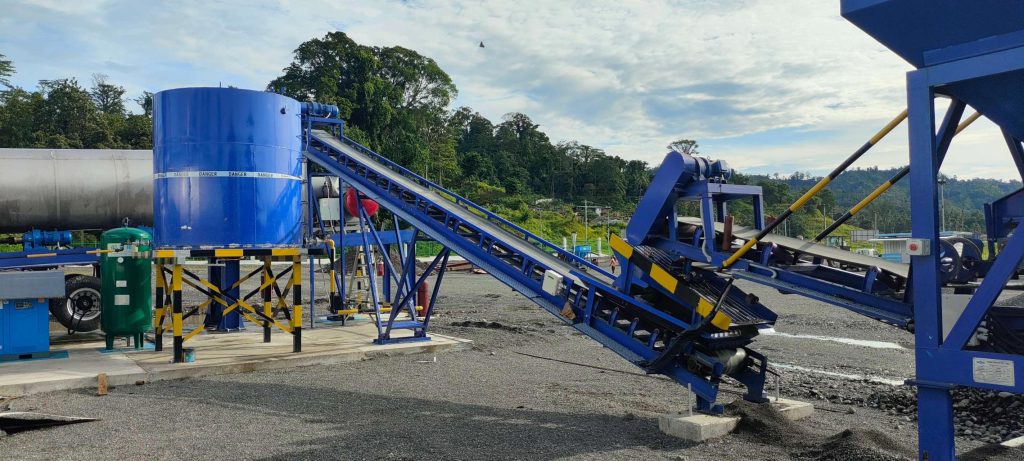
Conclusion
In summary, the differences in finished mixture storage methods and transportation adaptability between asphalt mixing plants for precast construction and traditional road construction are significant. Traditional road construction relies on bulk storage silos and large tanker trucks, whereas precast construction necessitates specialized storage solutions and transportation methods tailored to specific project needs. Understanding these distinctions enables operators to optimize their processes, enhance efficiency, and ensure that both road and precast projects are executed successfully. As a well-qualified asphalt mixing plant manufacturer, Macroad has also taken this aspect into consideration. As the construction industry continues to evolve, recognizing and adapting to these differences will be crucial for maintaining competitive advantage and operational excellence.