In today’s rapidly developing world, high-quality asphalt plants play a crucial role in constructing and maintaining our transportation networks. From busy highways to local roads, the performance and durability of asphalt pavements directly impact our daily lives. This article explores the key factors influencing asphalt quality, compares different mixing technologies, and discusses the differences between various asphalt plants.
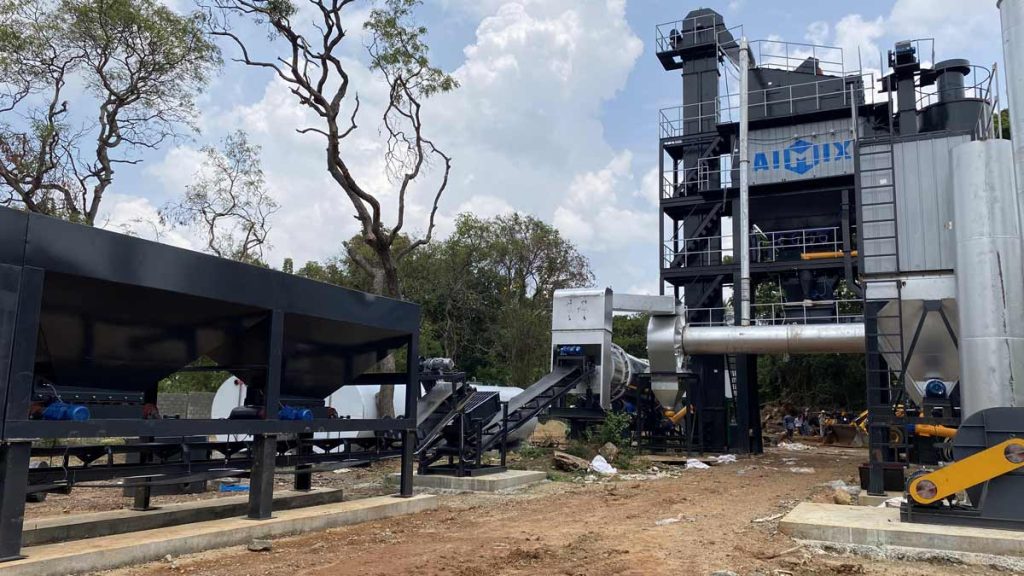
Core Factors Controlling Asphalt Quality
- The selection and quality of raw materials are fundamental to producing excellent asphalt. Aggregate gradation precision directly affects the density of the mixture, with particle size errors typically needing to be controlled within ±2%. The choice of high-quality aggregate ensures better load-bearing capacity and weather resistance of the pavement.
- The production process must be meticulously controlled. Modified agent addition ratios require dynamic monitoring through infrared spectroscopy to ensure uniform polymer distribution. This step is critical as it enhances the asphalt’s performance characteristics, such as elasticity and temperature stability.
- Advanced equipment is essential for consistent quality. The temperature control system must maintain a precise mixing zone temperature of 190-210℃. Temperature variations exceeding 5℃ can accelerate asphalt aging, reducing the pavement’s lifespan.
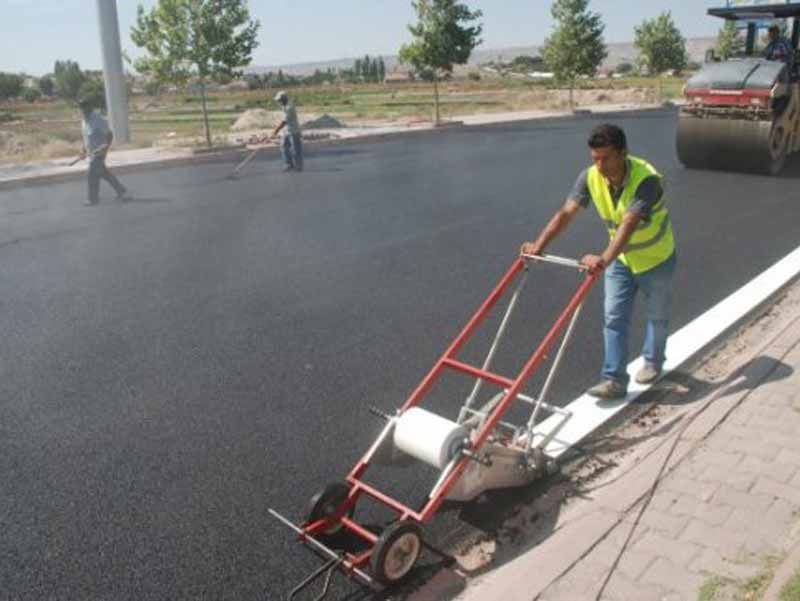
The Reason Why Asphalt Batching Plants Produce Higher Quality Asphalt Compared To Drum Mix Plants
The technology of asphalt batching plant offers significant advantages over traditional drum mixing. Utilizing a dual-shaft counter-rotational mixing principle, forced mixers achieve 40% higher efficiency and 99.2% material uniformity. Their thermal conduction systems feature triple insulation, extending mixture temperature retention by 2.5 hours.
Performance testing reveals substantial benefits. Marshall stability of forced-mixed asphalt reaches 12.5kN, an 18% improvement over drum-mixed products. Rutting tests demonstrate 22% less deformation, directly translating to longer-lasting pavements that better withstand heavy traffic loads.
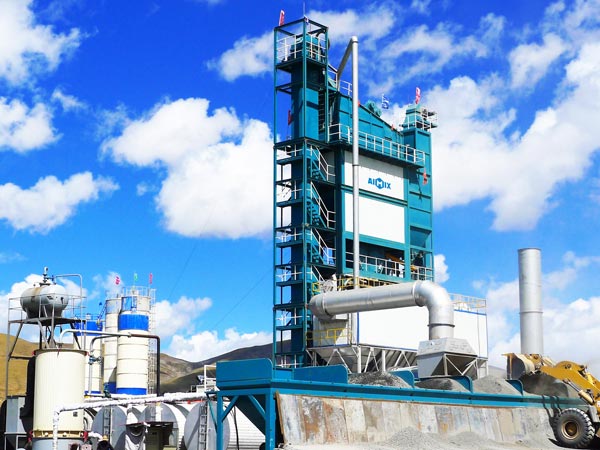
Mobile vs. Stationary Batch Asphalt Plants
Asphalt batching plants are divided into two types: mobile asphalt batching plants and stationary asphalt mixing plants.
- Mobile Asphalt Batching Plants:
- Offer exceptional flexibility with modular designs that can be assembled within 72 hours.
- Ideal for multi-section road projects where rapid deployment is necessary.
- Save 30% on civil construction costs compared to stationary plants.
- Consume 15% more fuel than their stationary counterparts.
- Equipped with advanced technologies for producing eco-friendly asphalt mixtures.
- Stationary Asphalt Mixing Plants:
- Excel in environmental performance with six-stage dust removal systems.
- Feature RAP (Reclaimed Asphalt Pavement) regeneration modules, allowing up to 45% recycled material usage.
- Suitable for eco-sensitive municipal projects with strict environmental regulations.
- Typically have higher production capacities and are better suited for large-scale, long-term projects.
- Require significant initial investment but offer lower operational costs over time.
Understanding the factors that influence asphalt quality helps project managers make informed decisions. Whether choosing between forced mixing and drum mixing technologies or deciding between mobile and stationary plant configurations, each decision impacts the final pavement performance. By prioritizing quality control throughout the production process and selecting appropriate technologies, we can build more durable, sustainable road networks that serve communities for decades.